We started the day with some conversation on why glue joints fail. There are many reasons that glue joints can fail and it only takes one misstep to make even the nicest looking joint come loose. However, we often find that there is at least one, if not many things wrong with some joints, and we need to learn how to respond to these situations. Our 1st step is learning about how our furniture is constructed.
Monday, November 23, 2009
Wood 1007 Methods of Fastening: Day One
We started the day with some conversation on why glue joints fail. There are many reasons that glue joints can fail and it only takes one misstep to make even the nicest looking joint come loose. However, we often find that there is at least one, if not many things wrong with some joints, and we need to learn how to respond to these situations. Our 1st step is learning about how our furniture is constructed.
Thursday, November 19, 2009
Wood 1004 Wood Working: Veneer Patching
Wednesday, November 4, 2009
Wood 1004 Woodworking: Begining a New Chapter Again
Thursday, October 29, 2009
Wood 1019 Spot Repair II: NIWF Tours Schneiderman's Distribution Center
Wednesday, October 28, 2009
Wood 1019 Spot Repair II: Class of 2010 visits HOM Furniture
Working out in the real world gives the students a first hand view of what they might face on a day to day basis once they leave DCTC. Some of the Employees at HOM are past graduates of the program so they speak the same language of wood finishing. This unique experience helps to shape the students knowledge of some of the careers that may be opening up to them as graduates of the National Institute of Wood Finishi
Tuesday, October 27, 2009
Wood 1019 Spot Repair II: NIWF Does Conservation Work at Historic Fort Snelling Chapel
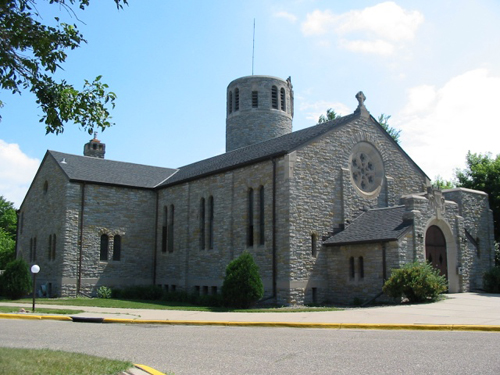
We were guided by past NIWF grad, Travis Beard, who volunteers on the Fort Snelling Memorial Chapel Foundation, and has been working in the chapel for a while, cleaning and restoring the woodwork, carvings and wooden statues.
Monday, October 26, 2009
Another Testimonial From a Past Grad
"In May of 1997, I attended a woodworking trade show in Little Rock, AR. It was through this show that I made a chance contact with a former graduate of the DCTC Wood Finishing Technology Program. The successful graduate explained the course work, skill sets learned, and the joy of knowing how to repair furniture. From this meeting, I was inspired to contact Mitch Kohanek at DCTC.
I graduated the Wood Finishing Technology Program at DCTC in June of 1998.
After graduating from the Wood Finishing Technology Program at DCTC, I was employed with a high end commercial furniture dealer in the Twin Cities area. My position was Manager, Restoration Services. I was tasked with starting a furniture service department at this company. Upon the completion of 2.5 years of employment, I was given the opportunity to purchase all of the assets of the service department and provide service through a sub-contractor arrangement.
In mid 2001, I relocated back to north central Arkansas, the area where I was raised. I started a furniture services company in Harrison, AR. My services include furniture refinishing, pre-finishing, and furniture touch-up, serving both commercial and residential customers.
The skill sets I learned at DCTC from Mitch Kohanek has allowed me to repair and finish anything with great confidence. All of the technical skills learned at DCTC Wood Finishing Technology Program are applied in my current business.
Mitch Kohanek is an inspiring teacher who can communicate his skills to those who care to learn."
Thursday, October 22, 2009
Wood 1019 Spot Repair II: Joe Renchin Spends the Day Talking Upholstery
Tuesday, October 20, 2009
Wood 1019 Spot Repair II: Ken Norgard Visits to Demonstrate Leather & Vinyl Repair
Monday, October 12, 2009
Wood 1019 Spot Repair II: Jerry Behrens visits DCTC again to talk touch-up
Friday, October 9, 2009
Wood 1019 Spot Repair II: Past Grad Dave Smith, Guest lecturing at DCTC
Next he painted in the background color.
Throughout the year, we continue to learn techniques like these, and it's always a pleasure to have past grads come in to show their skills! Thanks Dave!
Thursday, October 8, 2009
A Testimonial From a Past Graduate

After graduation I worked for a refinishing shop that readily employed NIWF graduates because the owner knew the graduates were qualified, professional, and required little training. This employment was valuable in that it taught me the real world of furniture finishing as a business. That is, dealing with customers, how to make a profit, and what it takes to run a finishing business.
I moved to Virginia 4 years later and started my own business. Make no mistake; this was not easy. I now have the largest finishing shop in my town. I have 4 wonderful employees who love the work as I do. We are still struggling but business gets better each year.
Because of NIWF, I have the most rewarding career. I and my employees enjoy coming to work every day.
Dick Patch
2000 Graduate
Roanoke VA
Wednesday, September 30, 2009
Wood 1015 Spot Repair I: HOM Furniture visits DCTC to demonstrate spot repair technique
It is always gratifying to see past students become the professionals and to watch them teach the new group of future pros!
Saturday, September 26, 2009
Wood 1015 Spot Repair I: French Padding Color


We can apply pigment to the wood, then use a French Padding technique to lock in the color.

Tuesday, September 22, 2009
Wood 1015 Spot Repair I: Fixing vertical surfaces
The techniques we use for vertical repairs are the same as any other, but the mechanics of it change as our range of motion can become limited, and gravity takes hold of our materials.
Saturday, September 19, 2009
Wood 1015 Spot Repair I: Repairing a scratch
Monday, August 31, 2009
Wood 1012 Color Theory - Using New Mediums

In the first picture, you can see we are color matching, that is to say, the students are given a sample of wood and asked to find a mixture of colorants that will match. Currently we are using glazes to find that match, but in the near future, we will use powdered pigments, dyes as well as using different glazing and toning techniques to achieve a match.
Sunday, August 30, 2009
2009-2010 School Year Begins
Wood 1012 Color Theory
Wood 1015 Spot Repair I
Wood 1019 Spot Repair II
Wood 1004 Wood Working
Wood 1007 Methods of Fastening
Wood 1010 Wood and Finishing Technology
Wood 1026 Advanced Finishing
Wood 1032 Furniture Conservation
Wood 1021 Wood Refinishing
Each course is approximately 17 working days and is set up in a way that one could take just one or two courses, please refer to the DCTC catalog for more information on classes that might have a pre-requisite at www.DCTC.edu
Most of the blog posts will be titled with the corresponding class, so if you want to know what goes on in any of these classes, stay tuned and see first hand what and how we learn! And be sure to go back in the blog are read about last year.
On a side note, NIWF offers a Furniture Service Technician certificate program for completing the first three courses (Color Theory, Spot Repair I & Spot Repair II). Furniture Service Technicians repair minor damage (referred to as spot repair) to wood, vinyl, leather and fabric. Spot repair usually involves (but is certainly not limited to) repairs such as minor water damage, scratches, nicks, dents, cigarette burns, or even a fairly large damaged area such as the corner of a table. These repairs are made by filling the void with a solid material and applying color to it, matching the surrounding area. Leather and vinyl repair is done much the same way. Upholstery can be repaired without having to re-upholster the entire piece.Furniture refurbishing means cleaning (instead of stripping) furniture and furniture maintenance (polishing and waxing).Furniture Service Technicians may work at the customer's home site, in furniture stores, or in a workshop. Possible job opportunities include self-employment, furniture stores or outlets, or an existing furniture service business. While total furniture restoration requires a workshop setting, the Furniture Service Technician can work from a small toolbox.
Friday, July 24, 2009
Wood 1026 Advanced Finishing: Don Williams in for summer seminar on Restoration, Chemistry and Technology of Transparent Furniture Coatings
*The History of Coatings - What Was It Originally?
*Technology of Materials and Processes - What Is It, and How Do we Know?
*What Will We do About It - Treatment Decisions and Processes
Some of the specifics that were covered were:
*Introduction to Coatings Chemistry and Technology: Formulation and Film Formation
*Historic and Contemporary Wood finishing Materials and Techniques
*Solvent Theory and Solubility Practice
*Evaluation of Appearance
*Characterization of Historic Coatings
*Survey of Coating Resins Used in Conservation
*Natural and Synthetic Dyes for Furniture Finishes
*Strategic Techniques for Coatings Restoration and Preservation
A subsequent coatings course (July 2010, proposed) will emphasize painted finishes, e.g. poly-chrome sculpture, decorated furniture finishes, and consolidating and inpainting painted surfaces. A third course in the series is tentatively scheduled for July 2011, and will emphasize advanced applications in the workshop setting.
Thursday, July 23, 2009
Master Finisher, Greg Johnson teaches workshop at DCTC & NIWF
Wednesday, July 22, 2009
Past Grad, Sean Harrigan Talks About His Experience at NIWF
Upon re-entering the workforce, I am slowly building my own Wood Finishing business. Now contracting on-site wood finishing work, I feel I have an edge over the local competition. I’ve executed successful spot repairs and attractive interior finishes. I am able to offer many finishing solutions and options on projects old and new from furniture to architectural millwork. My knowledge from N.I.W.F. is used on a daily basis. Everyday I think of new ideas and I am impressed how far this education has already taken me.
Mitch Kohanek is inspiring, passionate and dedicated to teaching you the art and craft of wood finishing. He has instilled in me a level of confidence and a thirst to seek out and learn more about finishing. This program is one of a kind. It has enhanced my quality of life immeasurably. Thanks Mitch. I’ll see you at one of your summer offerings."
Tuesday, June 2, 2009
Past Grad & Advisory Board member, Tammy Wold visits

Past Grad, Tammy Wold, came to visit and talk about spraying technique. Tammy graduated in 1980, and was hired on as a touch-up and repair tech at a furniture company in St. Paul, MN where she worked for 2 years. In 1982 she worked as a subcontractor doing refinishing of furniture and residential kitchens. In 1983 she went to work for a refinishing company in St. Paul until 1986 when she opened a small business in Maple Grove, MN. Their main work was prefinishing for other businesses in the industry, cabinetmakers, furniture makers, and store fixture manufactures. In 1998 Tammy went to work as a supervisor of the finishing department for Nevers Industries, a company that manufactures conference room furniture to order. We are also honored to have Tammy as a member of the Dakota County Technical College Advisory Committee, which she joined in 1999.
Monday, May 18, 2009
Wood 1021 Wood Refinishing: Glazing Color
Wood 1026 Advanced Finishing: High Gloss Buffing
Friday, May 15, 2009
Wood 1032 Furniture Conservation: A Visit with Paul Storch, Senior Objects Conservator at the MN Historical Society
Wednesday, April 22, 2009
Wood 1021 Wood Refinishing: Putting it all together
There is a great pride that can be taken in the knowledge that you began a project, planned it out, can justify your decisions and have a beautiful piece of furniture at the end of the process!